NCERT Solutions, Question Answer and Mind Map for Class 12 Chemistry Chapter 15, “Polymers,” is a study material package designed to help students understand the various types of polymers, their properties, and their applications in everyday life.
The NCERT Solutions provide detailed explanations and answers to the questions presented in the chapter. The solutions cover all the topics in the chapter, including the classification of polymers, their molecular structure, and their properties, such as mechanical, electrical, and optical properties. They also provide tips on how to answer different types of questions, including short answer, long answer, and multiple-choice questions.
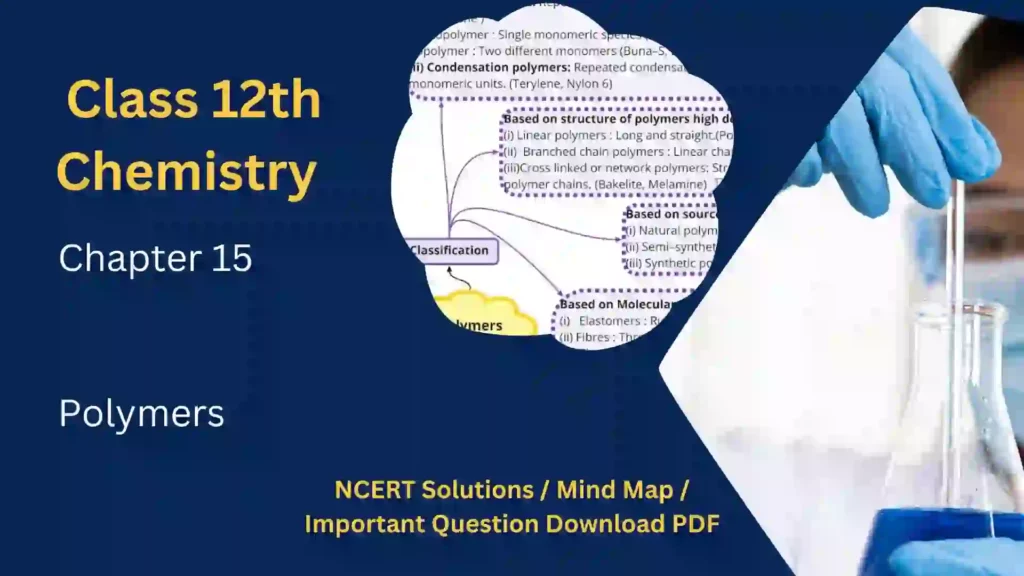
The question-answer section of the chapter covers a wide range of topics, from the various types of polymers, such as addition, condensation, and copolymers, to the properties of polymers, such as their molecular weight and their glass transition temperature. It also includes questions on the applications of polymers in various fields, such as packaging, textiles, and medicine.
The mind map provides a visual representation of the key topics covered in the chapter, allowing students to understand the connections between different concepts and ideas. The mind map covers the classification of polymers, their molecular structure, and their properties.
NCERT Solution / Notes Class 12 Chemistry Chapter 15 Polymers with mind Map PDF Download
Polymer
- The word ‘polymer’ is coined from two Greek words.
- Poly = Many and Mer =unit or part
- They are also called as macromolecules which are formed by joining of repeating structural units on a large scale.
Monomer
The repeating structural units which are derived from some simple and reactive molecules are known as monomers.
They are linked to each other by covalent bonds.
Polymerisation
The process of formation of polymers from respective monomers is called polymerisation. Examples:
- Conversion of ethene to polyethene

Define the terms: Monomers, Polymers & Polymerization
Define the terms: Monomers, Polymers & Polymerization
The term polymer is defined as a chemical substance of a very high molecular mass (103-107u) formed by combination of a simple molecule, called monomers.
Polymers are also known as macromolecules, which are formed by repeating structural units on large scale.
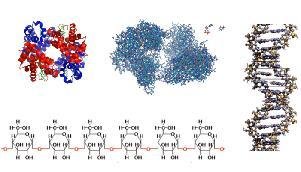
This process of formation of polymers from respective monomers is called polymerisation.
For example:- n CH2 = nCH2–> n[-CH2 – CH2 – ] –> [-CH2-CH2-] n
Ethene Repeating Unit Polythene polymer
Classification of Polymers
Classification of Polymers
There are several ways of classification of polymers based on some special considerations.
The following are some of the common classifications of polymers:
- Source
- Structure
- Mode of polymerization
- Molecular Force
Source
Under this type of classification, there are three sub categories.
Natural polymers
These polymers are found in plants and animals. Examples are proteins, cellulose, starch, some resins and rubber.
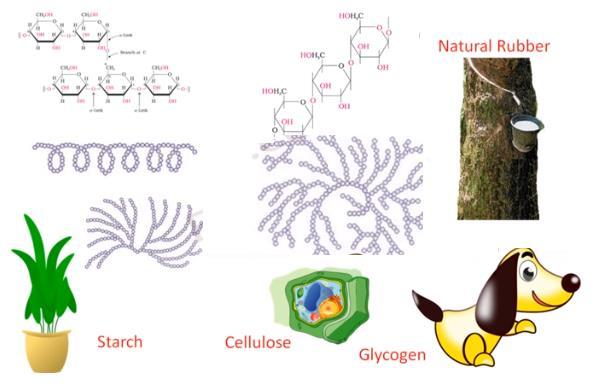
Semi-synthetic polymers
b) Cellulose derivatives as cellulose acetate (rayon) and cellulose nitrate, etc. are the some examples.
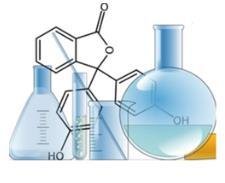
Synthetic Polymers
A variety of synthetic polymers as plastic (polythene), synthetic fibres. Examples: – (nylon 6, 6) and synthetic rubbers (Buna – S) are polymers extensively used in daily life as well as in industry.
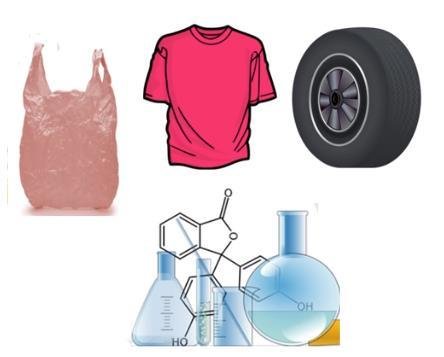
Structure
There are three different types based on the structure of the polymers.
Linear Polymers: –
These polymers consist of long and straight chains. The examples are high density polythene, polyvinyl chloride, etc. These are represented as:

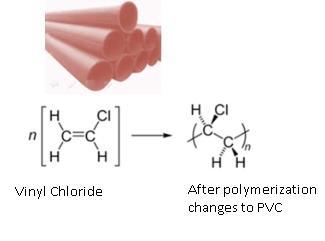
Branched-chain polymers:-
b) These polymers contain linear chains having some branches, e.g. low density polythene. These are depicted as follows:

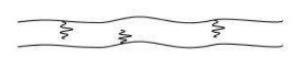
Cross-linked or Network polymers:-
c) These are usually formed from bi-functional and tri-functional monomers and contain strong covalent bonds between various linear polymer chains, e.g. Bakelite, melamine, etc. These polymers are depicted as follows:
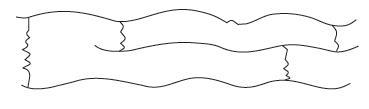
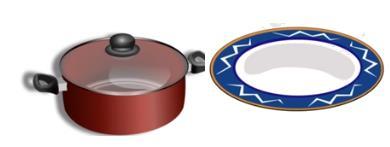
Mode of Polymerization
Polymers can also be classified on the basis of mode of polymerisation into two sub groups.
Addition polymers: –
- The addition polymers are formed by the repeated addition of monomer molecules possessing double or triple bonds.
- For example: – The formation of polythene from Ethene and polypropene from propene.
- However, the addition polymers formed by the polymerisation of a single monomeric species are known as homopolymers.
- For example: – polythene.
n CH2 = CH2 –> (CH2-CH2-)n Homopolymer
Ethene Polythene
The polymers made by addition polymerisation from two different monomers are termed as copolymers, e.g., Buna-S, Buna-N, etc.
nCH2 = CH – CH = CH2 + n C6H5CH = CH2 à (- CH2 – CH = CH – C6H5 – CH2 – CH – CH2 – )n
1,3 – Butadiene Styrene Butadiene-styrene copolymer
(Buna-S)
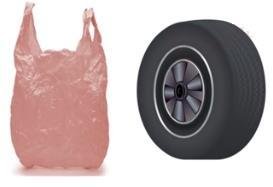
Condensation polymers
- The condensation polymers are formed by repeated condensation reaction between two different bi-functional or tri-functional monomeric units.
- In these polymerisation reactions, the elimination of small molecules such as water, alcohol, hydrogen chloride, etc. take place.
- The examples are Terylene (Dacron), nylon 6, 6, nylon 6, etc.
- For example, nylon 6, 6 is formed by the condensation of hexamethylene diamine with adipic acid.
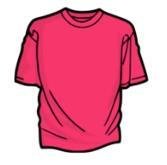
D. Molecular Forces
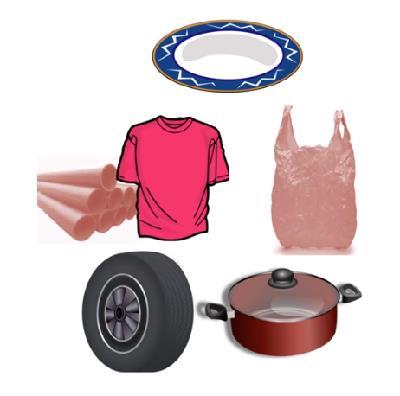
A large number of polymers can be used in different fields because of their mechanical properties like tensile strength, elasticity, toughness etc.
These mechanical properties are governed by intermolecular forces, e.g., van der Waals forces and hydrogen bonds, present in the polymer. These forces also bind the polymer chains.
The polymers are classified into the following four sub groups on the basis of magnitude of intermolecular forces present in them.
a) Elastomers: –
These are rubber – like solids with elastic properties.
The polymer chains are held together by the weakest intermolecular forces. These weak binding forces permit the polymer to be stretched.
A few ‘crosslinks’ are introduced in between the chains, which help the polymer to retract to its original position after the force is released as in vulcanised rubber. The examples are Buna-S, Buna-N, neoprene, etc.
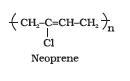
b) Fibres:-
Fibres are the thread forming solids which possess high tensile strength and high modulus.
These characteristics can be attributed to the strong intermolecular forces like hydrogen bonding.
These strong forces also lead to close packing of chains and thus impart crystalline nature. The examples are polyamides (nylon 6, 6), polyesters (terylene), etc.
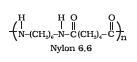
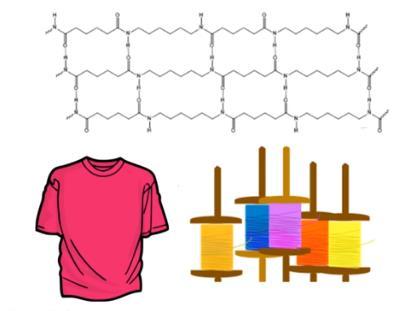
c) Thermoplastic Polymers:-
These are the linear or slightly branched long chain molecules capable of repeatedly softening on heating and hardening on cooling.
These polymers possess intermolecular forces of attraction intermediate between elastomers and fibres.
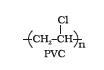
d) Thermosetting Polymers:-
These polymers are cross linked or heavily branched molecules, which on heating undergo extensive cross linking in moulds and again become infusible.
These cannot be reused. Some common examples are Bakelite, urea-formaldehyde resins, etc.
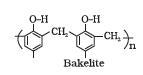
Types of Polymerisation Reactions
Addition or chain growth polymerisation
- In addition polymerisation, the molecules of the same monomer or different monomers add together on a large scale to form a polymer.
- The most common mechanism for addition polymerisation reactions is free radical mechanism.
- The steps involved are as follows:
Step 1:
Chain initiating step: Organic peroxides undergo homolytic fission to form free radicals which act as an initiator. The initiator adds to the C—C double bond of an alkene molecule to form a new free radical.
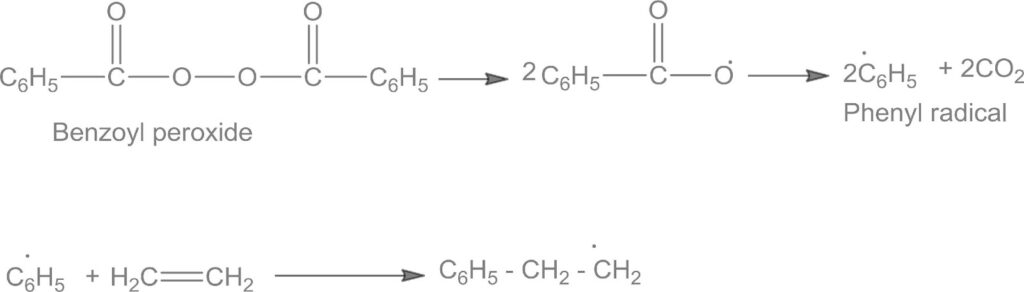
Step 2:
Chain propagating step: Free radicals formed by homolytic cleavage add to a double bond of
monomer to form a larger free radical. Radicals formed add to another alkene molecule to form a larger free radical. This process continues until the radical is destroyed. These steps are called propagation steps.
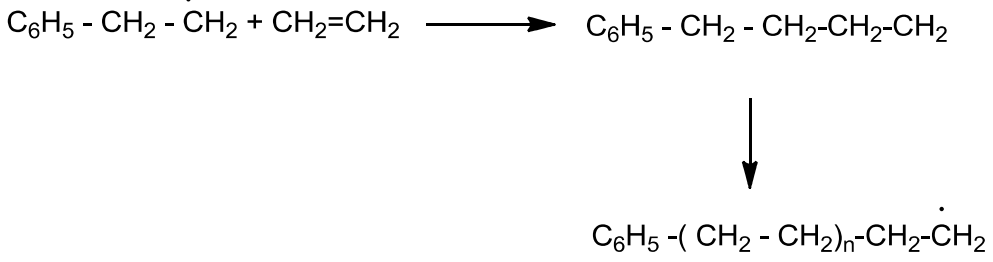
Step 3:
Chain terminating step: For termination of the long chain, free radicals combine in different ways to form polythene. One mode of termination of chain is shown below.
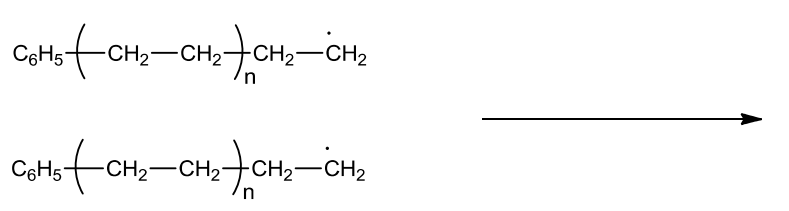
`

Addition polymerisation is called chain growth polymerisation because it occurs through stages leading to increase in chain length, and each stage produces reactive intermediates for use in the next stage of the growth of the chain.
Preparation of some important addition polymers
1. Low density polythene
- It is obtained by the polymerisation of ethene under high pressure of 1000-2000 atmospheres at a temperature of 350 K to 570 K in the presence of traces of dioxygen or a peroxide initiator (catalyst).
- It is a poor conductor of electricity and hence it is used as an insulator in electrical wires and manufacture of squeeze bottle, toys and flexible pipe.

2. High density polythene
- It is formed when addition polymerisation of ethene takes place in a hydrocarbon solvent in the presence of a catalyst such as triethylaluminium and titanium tetrachloride at a temperature of 333 K to 343 K and under a pressure of 6-7 atmospheres.
- It is used to manufacture buckets, dustbins, bottles, pipes etc.

2. Polytetrafluoroethene (Teflon)
- It is synthesized by heating tetrafluoroethene with a free radical or persulphate at high pressures.
- It is used in making oil seals and gaskets and also used for non-stick surface-coated utensils.
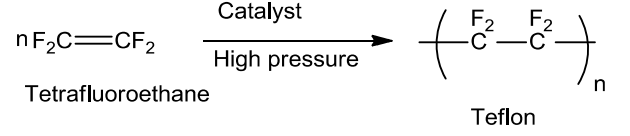
3. Polyacrilonytrile
- It is prepared by the addition polymerisation of acrylonitrile in presence of a peroxide catalyst.
- It is used as a substitute for wool in making commercial fibres as orlon or acrilan.
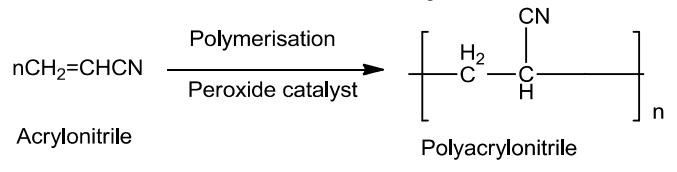
Condensation or step-growth polymerisation
- In this type of polymerisation, there is a repetitive condensation reaction between two bi-functional monomers with the loss of some simple molecules like water leading to the formation of high molecular mass condensation polymers.
- The product of each step is again a bi-functional species and the sequence of condensation goes on.
- Since each step produces a distinct functionalised species and is independent of each step, this process is called as step growth polymerisation.
- Interaction of ethylene glycol and terephthalic acid leading to the formation of terylene is an example of this type of condensation.
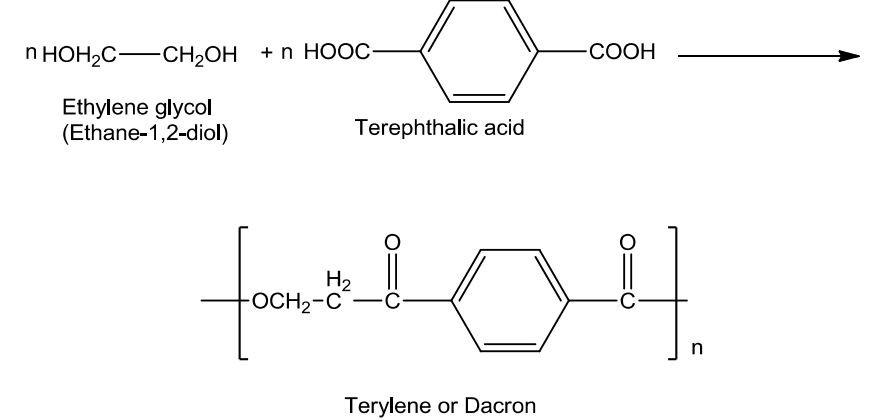
Some Important Condensation Polymerisation
- Polyamides
Nylons are polymers possessing amide linkages and are important examples of synthetic fibres. They are prepared by condensation polymerisation of diamines with dicarboxylic acids and also of amino acids and their lactams.
Preparation of Nylons
- Nylon 6,6
- It is prepared by the condensation polymerisation of hexamethylenediamine with adipic acid under high pressure and at high temperature.
- It is used in making sheets, bristles for brushes and in textile industry.

- Nylon 6
- It is obtained by heating caprolactum with water at a high temperature.
- It is used for the manufacture of tyre cords, fabrics and ropes.
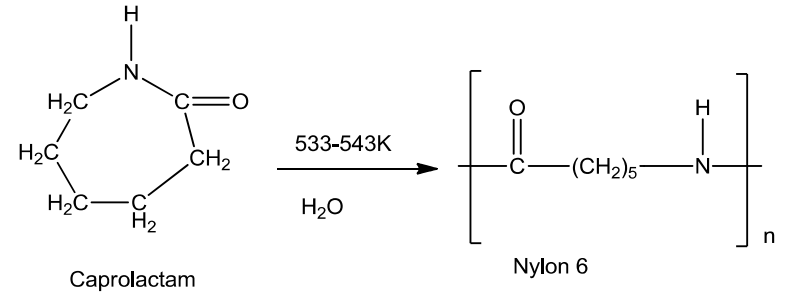
- Polyesters
- It is manufactured by heating a mixture of ethylene glycol and terephthalic acid at 420 to 460K in the presence of zinc acetate-antimony trioxide catalyst.
- Dacron or terylene is an example of polyester which is crease resistant and is used in blending with cotton and wool fibres and also as glass reinforcing materials in safety helmets etc.
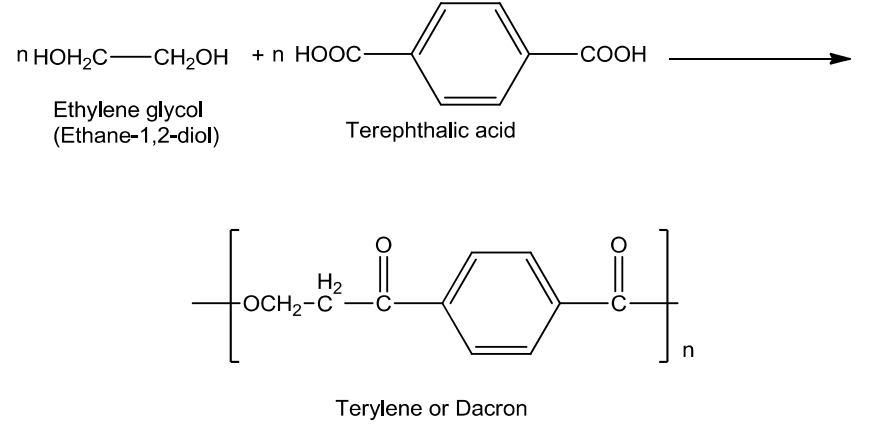
- Phenol-formaldehyde polymer(Bakelite and related polymers)
- It is obtained by the condensation reaction of phenol with formaldehyde in the presence of either an acid or a base catalyst.
- The reaction proceeds with the initial formation of o-and/or p-hydroxymethylphenol derivatives which further react with phenol to form compounds having rings joined to each other through — CH2 groups.
- The initial product could be a linear product — Novolac used in paints.
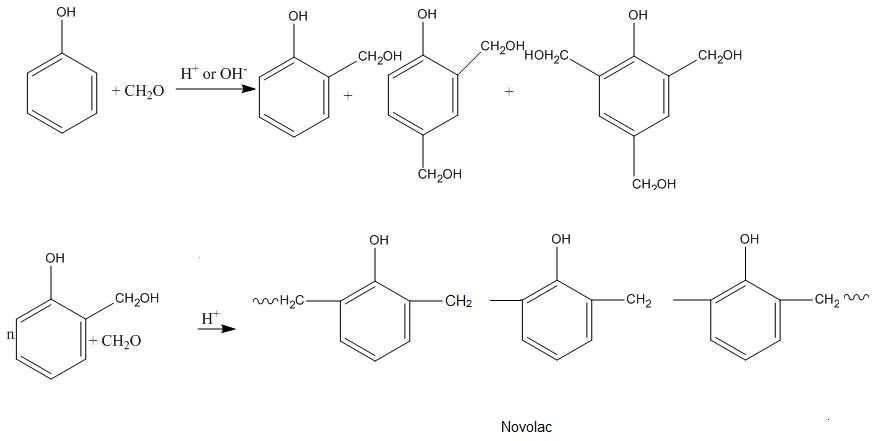
- Novolac on heating with formaldehyde undergoes cross linking to form infusible solid mass called Bakelite.
- It is used for making combs, phonograph records, electrical switches and handles of various utensils.
- Melamine-formaldehyde polymer
It is formed by the condensation polymerisation of melamine and formaldehyde.
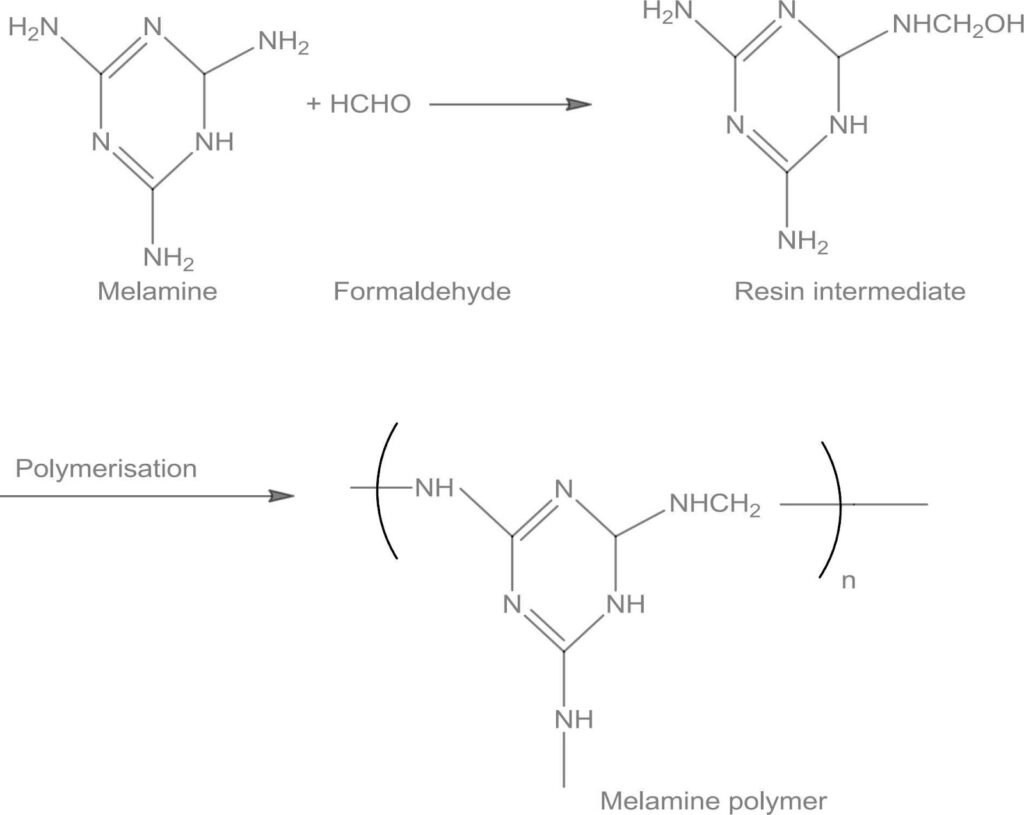
It is used in the manufacture of unbreakable crockery.
Copolymerisation
- It is a polymerisation reaction in which a mixture of more than one monomeric species is allowed to polymerise and form a polymer.
- The copolymer can be prepared by both chain growth polymerisation and step growth polymerisation.
- It contains multiple units of each monomer used in the same polymeric chain.
- A mixture of 1, 3-butadiene and styrene can form a polymer.
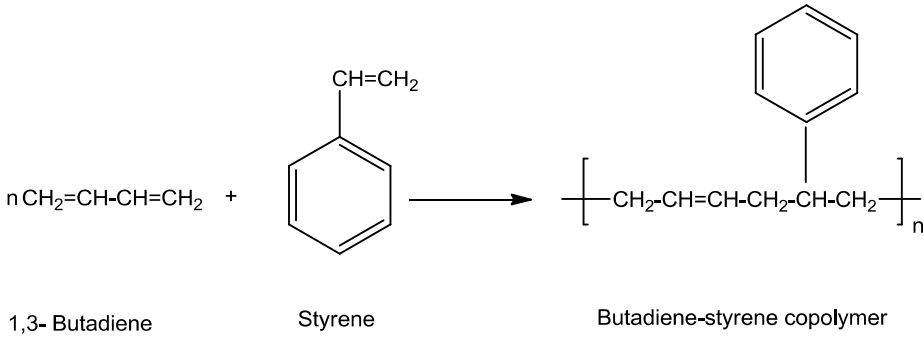
- Copolymers have properties quite different from homopolymers.
- Butadiene-styrene copolymer is quite tough and is a good substitute for natural rubber.
- It is used for the manufacture of auto tyres, floor tiles, footwear components, cable insulation etc.
Rubber
- Natural Rubber
- It is prepared from rubber latex which is a colloidal dispersion of rubber in water.

- It can be considered as a linear polymer of isoprene (2-methyl-1, 3-butadiene) and is also called as cis-1, 4-poIyisoprene.
Vulcanization of Rubber
- This process is used to improve the physical properties of rubber.
- In this process, mixture of raw rubber is heated with sulphur and appropriate additive at a temperature range between 373 K to 415 K.
- On vulcanisation, sulphur forms cross links at the reactive sites of double bonds and thus the rubber gets stiffened.
- Only 5 % of sulphur is used as a cross linking agent in the manufacture of tyre rubber.
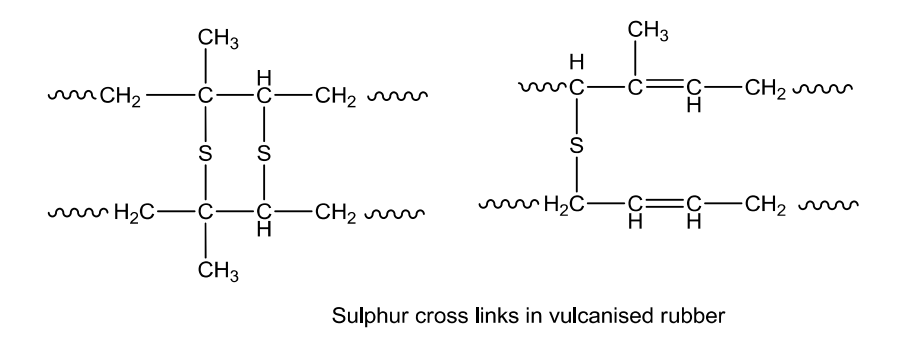
- Synthetic Rubbers
- It is a vulcanisable rubber like polymer.
- It is stretchable to twice its length and returns to its original shape and size as soon as the external force is released.
- Thus synthetic rubbers are either homopolymers of 1, 3-butadiene derivatives or copolymers of 1, 3-butadiene or its derivative with another unsaturated monomer.
Preparation of Synthetic Rubbers
- Neoprene
- Neoprene or polychloroprene is prepared by the free radical polymerisation of chloroprene.

- It is used for manufacturing conveyor belts, gaskets and hoses.
- Buna – N
- It is prepared by the copolymerisation of 1, 3-butadiene and acrylonitrile in the presence of a peroxide catalyst.
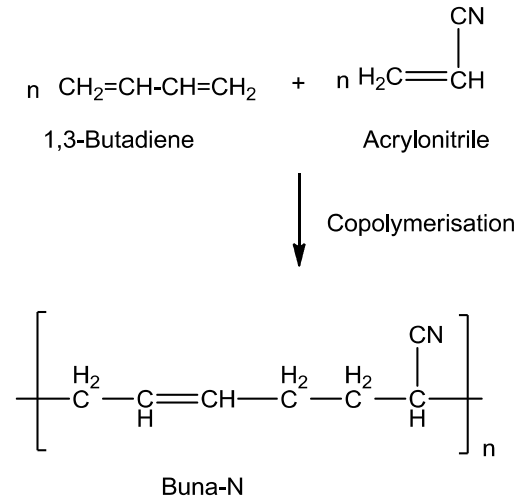
- It is used in making oil seals, tank lining etc. because it is resistant to the action of petrol, lubricating oil and organic solvents.
Molecular Mass of Polymers
- The polymer sample contains chains of varying lengths and hence its molecular mass is always expressed as an average.
- The molecular mass of polymers can be determined by chemical and physical methods.
Biodegradable Polymers
- Polymers which are degraded by microorganisms within a suitable period so that biodegradable polymers and their degraded products do not cause any serious effects on the environment.
- Certain new biodegradable synthetic polymers have been designed and developed.
- These polymers contain functional groups similar to the functional groups present in biopolymers.
- Aliphatic polyesters are one of the important classes of biodegradable polymers.
- Examples of biodegradable polymers:
- Poly–hydroxybutyrate-co–hydroxyl-valerate (PHBV): It is obtained by the copolymerisation of 3-hydroxybutanoic acid and 3-hydroxypentanoic acid.
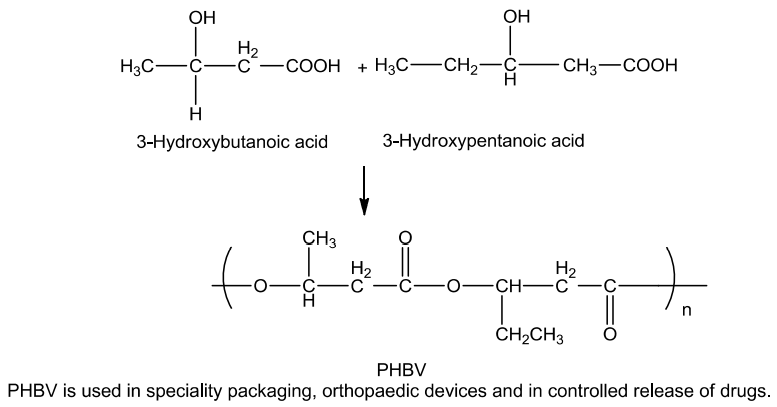
- Nylon 2—nylon 6: It is an alternating polyamide copolymer of glycine (H2N—CH2—COOH) and amino caproic acid (H2N (CH2)5 COOH.
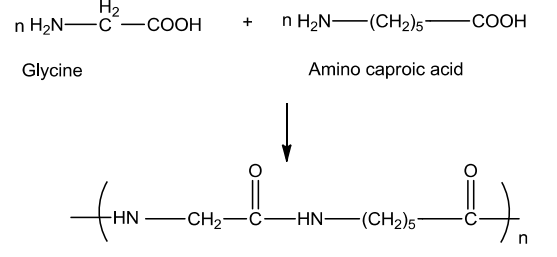
Preparation of Important Addition Reaction
Polyamides:-
These polymers possessing amide linkages are important examples of synthetic fibres and are termed as nylons. The general method of preparation consists of the condensation polymerisation of diamines with dicarboxylic acids and also of amino acids and their lactams.
Preparation of Nylons
Nylon 6, 6:-
It is prepared by the condensation polymerisation of hexamethylenediamine with adipic acid under high pressure and at high temperature.
Nylon 6, 6 is used in making sheets, bristles for brushes and in textile industry.
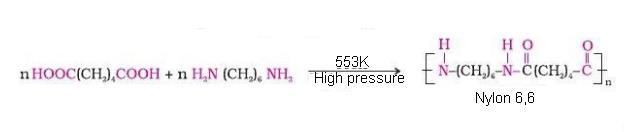
Nylon 6:-
It is obtained by heating Caprolactum with water at a high temperature.
Nylon 6 is used for the manufacture of tyre cords, fabrics and ropes.
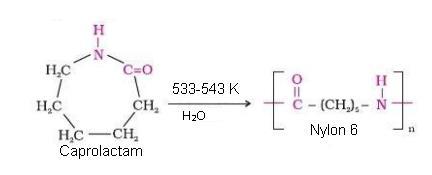
Polyesters: – These are the poly condensation products of dicarboxylic acids and diols.
Dacron or Terylene is the best known example of polyesters. It is manufactured by heating a mixture of ethylene glycol and terephthalic acid at 420 to 460 K in the presence of Zinc acetate antimony trioxide catalyst.
Dacron fibre (Terylene) is crease resistant and is used in blending with cotton and wool fibres and also as glass reinforcing materials in safety helmets, etc.
Phenol – formaldehyde polymer (Bakelite and related polymers):-
Phenol – formaldehyde polymers are the oldest synthetic polymers.
These are obtained by the condensation reaction of phenol with formaldehyde in the presence of either an acid or a base catalyst.
The reaction starts with the initial formation of o-and/or p-hydroxymethylphenol derivatives, which further react with phenol to form compounds having rings joined to each other through – CH2
The initial product could be a linear product – Novolac used in paints.
Novolac on heating with formaldehyde undergoes cross linking to form infusible solid mass called Bakelite. It is used for making combs, phonograph records, electrical switches and handles of various utensils.
Melamine- formaldehyde Polymer:-
Melamine formaldehyde polymer is formed by the condensation polymerisation of melamine and formaldehyde.
It is used in the manufacture of unbreakable crockery.
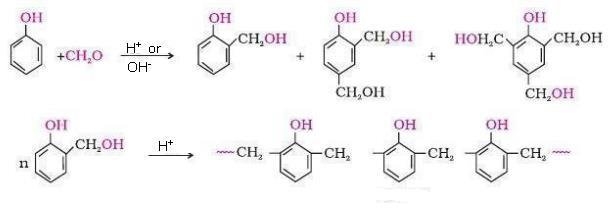
Novolac on heating with formaldehyde undergoes cross linking to form infusible solid mass called Bakelite. It is used for making combs, phonograph records, electrical switches and handles of various utensils.
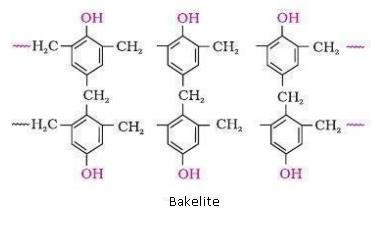
Melamine-formaldehyde Polymer:-
Melamine-formaldehyde polymer is formed by the condensation polymerisation of melamine and formaldehyde.
It is used in the manufacture of unbreakable crockery.
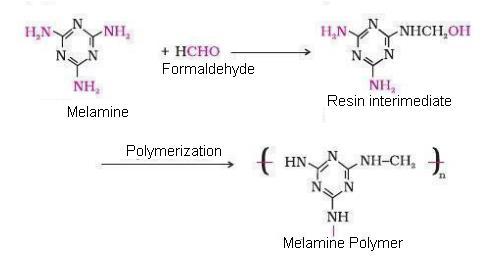
o Polymerization
Copolymerisation is a polymerisation reaction in which a mixture of more than one monomeric species is allowed to polymerise and form a copolymer.
The copolymer can be made not only by chain growth polymerisation but by step growth polymerisation also.
It contains multiple units of each monomer used in the same polymeric chain.
For example:-a mixture of 1, 3 – butadiene and styrene can form a copolymer.
Copolymers have properties quite different from homopolymers.
For example: – butadiene – styrene copolymer is quite tough and is a good substitute for natural rubber.
It is used for the manufacture of auto tyres, floor tiles, footwear components, cable insulation, etc.
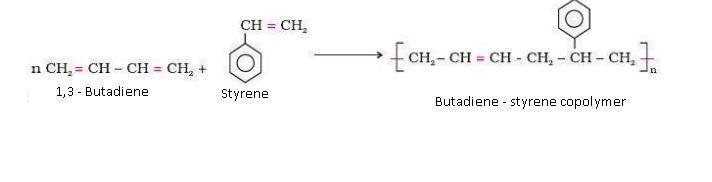
Rubber
Rubber is a natural polymer and possesses elastic properties.
It is also termed as elastomer and has a variety of uses.
It is manufactured from rubber latex which is a colloidal dispersion of rubber in water. This latex is obtained from the bark of rubber tree and is found in India, Sri Lanka, Indonesia, Malaysia and South America.
Natural Rubber
Natural rubber may be considered as a linear polymer of isoprene (2-methyl-1, 3-butadiene) and is also called as cis – 1, 4 -polyisoprene.
The cis-polyisoprene molecule consists of various chains held together by weak van der Waals interactions and has a coiled structure.
Thus, it can be stretched like a spring and exhibits elastic properties.
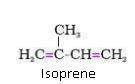
Vulcanization of Rubber:-
Natural rubber becomes soft at high temperature (>335 K) and brittle at low temperatures (<283 K) and shows high water absorption capacity.
It is soluble in non-polar solvents and is non-resistant to attack by oxidising agents. To improve upon these physical properties, a process of vulcanisation is carried out. This process consists of heating a mixture of raw rubber with sulphur and an appropriate additive at a temperature range 373 K to 415K.
On vulcanisation, sulphur forms cross links at the reactive sites of double bonds and thus the rubber gets stiffened.
In the manufacture of tyre rubber, 5% of sulphur is used as a crosslinking agent.
The probable structures of vulcanised rubber molecules are depicted below:
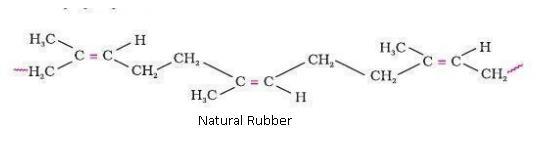
Synthetic Rubber
Synthetic rubber is any vulcanisable rubber like polymer, which is capable of getting stretched to twice its length.
However, it returns to its original shape and size as soon as the external stretching force is released.
Thus, synthetic rubbers are either homopolymers of 1, 3 – butadiene derivatives or copolymers of 1, 3 – butadiene or its derivatives with another unsaturated monomer.
Preparation of Synthetic Rubbers
Neoprene:-
Neoprene or poly chloroprene is formed by the free radical polymerisation of chloroprene.
It has superior resistance to vegetable and mineral oils.
It is used for manufacturing conveyor belts, gaskets and hoses.
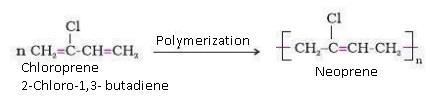
Buna –N:-
Buna –N is obtained by the copolymerisation of 1, 3 – butadiene and acrylonitrile in the presence of a peroxide catalyst.
It is resistant to the action of petrol, lubricating oil and organic solvents. It is used in making oil seals, tank lining, etc.

NCERT Solutions for Class 12 Chemistry chapter wise
- Chapter 1 The Solid State
- Chapter 2 Solutions
- Chapter 3 Electrochemistry
- Chapter 4 Chemical Kinetics
- Chapter 5 Surface Chemistry
- Chapter 6 General Principles and Processes of Isolation of Elements
- Chapter 7 The p Block Elements
- Chapter 8 The d and f Block Elements
- Chapter 9 Coordination Compounds
- Chapter 10 Haloalkanes and Haloarenes
- Chapter 11 Alcohols Phenols and Ethers
- Chapter 12 Aldehydes Ketones and Carboxylic Acids
- Chapter 13 Amines
- Chapter 14 Biomolecules
- Chapter 15 Polymers
- Chapter 16 Chemistry in Everyday Life